Calculation of Production Line Takt Time
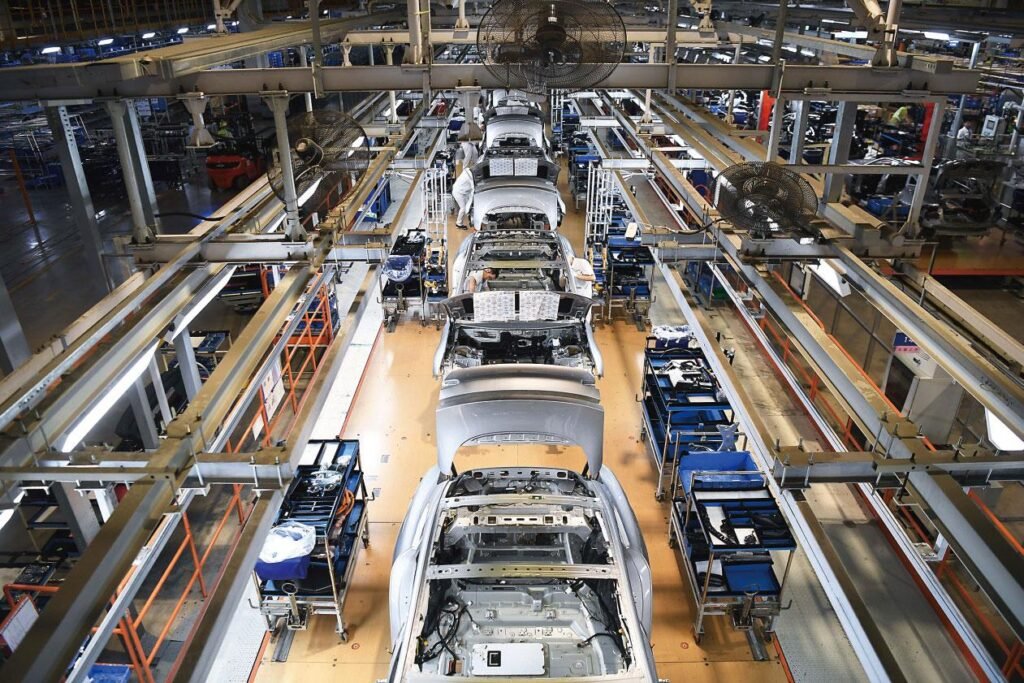
Reasonable Takt Time is crucial for production line efficiency, ensuring that the production pace of each workstation matches customer demand, thereby reducing waiting and idle times. It also helps balance the workload, preventing workstations from being overloaded or underutilized, and decreases work-in-progress inventory as production synchronizes with demand. Moreover, a stable production rhythm contributes to improved product quality by reducing errors caused by haste. Reasonable Takt Time enhances production flexibility, allowing the line to quickly adapt to changes in market demands. It optimizes resource utilization, ensuring that labor and equipment are used most effectively, and reduces the production cost per unit by minimizing waste and improving production efficiency. In summary, reasonable Takt Time is key to achieving lean production and enhancing overall production performance.
Here’s the explanation about calculating Takt Time and Capacity:
- Calculating Takt Time: Takt Time is the average time required to produce one product to meet customer demand. It can be calculated using the following formula: Takt Time=Available Working TimeDemandTakt Time=DemandAvailable Working Time Where:
- Available Working Time refers to the total time available for production within a certain period, usually measured in hours.Demand refers to the number of products customers need within the same period.
- Calculating Capacity: Capacity refers to the maximum number of products a production system can produce within a certain period. It can be calculated using the following formula: Capacity=Available Working TimeTakt TimeCapacity=Takt TimeAvailable Working Time Where:
- Available Working Time and Takt Time are defined as above.
These calculations provide a basis for basic production planning and scheduling. In practical applications, factors such as machine breakdowns, employee efficiency, and material supply may also affect actual capacity and Takt Time. Additionally, for more accurate production planning, more sophisticated production management software and tools may be required.
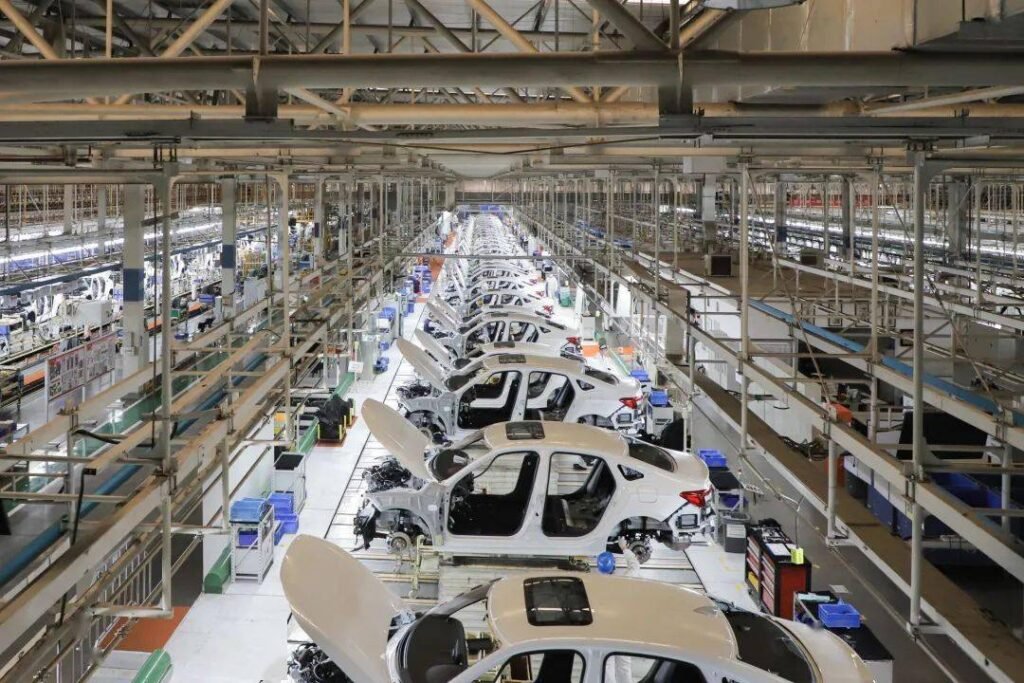
Determining a reasonable Takt Time on a production line typically involves the following steps:
- Understand Customer Demand:
- Determine the customer’s demand for the product, which can be daily, weekly, or monthly requirements.
- Calculate Available Working Time:
- Determine the total working time of the production line over a certain period, including regular working hours and possible overtime.
- Calculate Takt Time:
- Use the formula TaktTime=Available Working Time / Demand TaktTime=DemandAvailable Working Time to calculate the Takt Time.
- Consider Production Capacity:
- Assess the actual production capacity of the line to ensure it can meet the requirements of the Takt Time.
- Analyze the Production Process:
- Analyze each step of the production line to identify any bottlenecks or inefficient processes.
- Consider Production Variability:
- Account for potential fluctuations in the production process, such as equipment breakdowns or employee absences, which can affect Takt Time.
- Develop Buffer Strategies:
- To cope with production variability, it may be necessary to develop buffer strategies, such as additional working hours or backup resources.
- Continuous Monitoring and Adjustment:
- Continuously monitor the performance of the production line and adjust the Takt Time according to actual conditions.
- Use Lean Tools:
- Utilize lean production tools, such as Value Stream Mapping and 5S, to identify and eliminate waste and optimize the production process.
- Employee Training and Involvement:
- Train employees to ensure they understand the importance of Takt Time and encourage their participation in process improvement.
- Utilize Data and Analysis:
- Collect and analyze production data, using statistical methods to optimize Takt Time.
- Simulation and Testing:
- Before implementation, different Takt Time settings can be tested through simulation to predict their impact on production.
By following these steps, a reasonable Takt Time that meets both customer demand and the production line’s actual capabilities can be determined.