Electric Scooter Assembly Line Plant
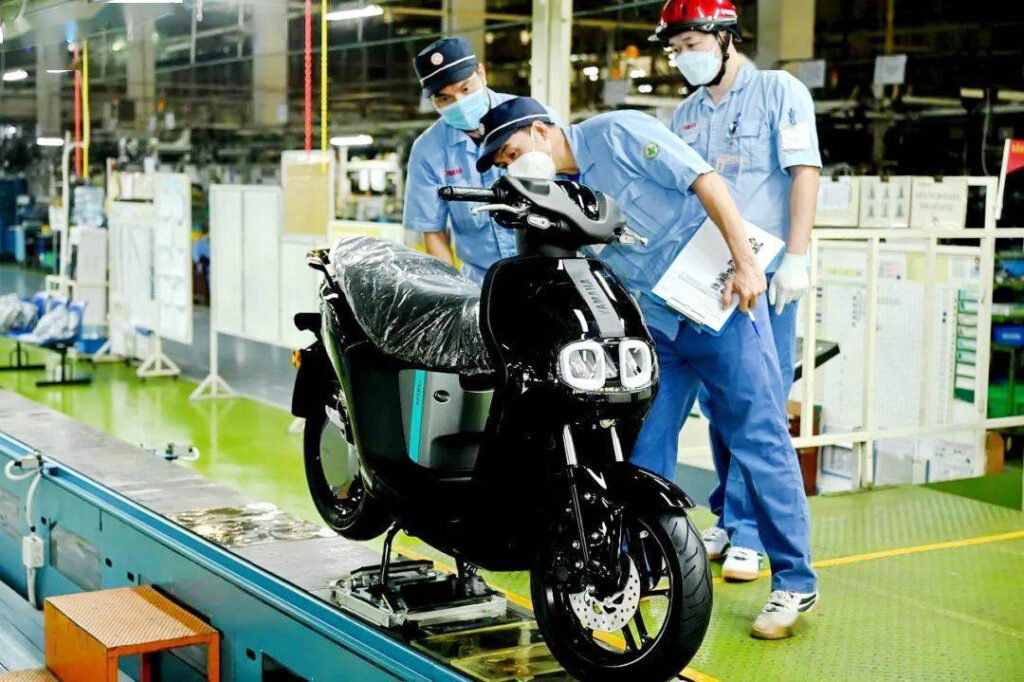
Electric scooter assembly lines significantly enhance production efficiency and product quality through automation and standardized operations. They reduce costs by minimizing human errors, material waste, and production cycles, while improving safety and flexibility in the manufacturing process. Additionally, assembly lines facilitate quality monitoring and data tracking, providing robust support for continuous improvement in production processes.

Electric scooter component processing equipment is crucial for ensuring the quality and performance of electric scooters. These devices typically include:
- Cutting and Welding Equipment: Used for precision machining of the metal frame and other structural parts of the electric scooter.
- Automated Assembly Lines: To improve assembly efficiency and ensure continuity and consistency in the production process.
- Electric or Pneumatic Tools: Used for various fastening and connecting tasks during assembly.
- Inspection and Testing Equipment: To assess the performance of electric scooters, including speed, endurance, and safety.
- Battery and Charger Testing Instruments: To ensure that these key components meet safety and performance standards.
The main components of an electric scooter also include the motor, battery, and controller. The motor provides power, the battery stores energy, and the controller manages the operation of the motor, enabling acceleration, deceleration, and directional control. With technological advancements, these components and corresponding processing equipment are continuously being updated and optimized to meet higher production efficiency and quality requirements.

The final assembly process of an electric scooter is a critical phase that ensures the quality and performance of the final product. It typically includes the following detailed steps:









- Preparation Work: Before starting the final assembly, ensure that all components are ready and meet quality standards, including the frame, motor, battery, controller, wheels, lights, etc.
- Frame Assembly: The frame is the basic structure of the electric scooter, usually welded from metal tubes. On the assembly line, the frame is placed on the assembly platform, ready for the installation of other parts.
- Motor Installation: The motor is the power source of the electric scooter, typically installed in the central position of the frame. The installation of the motor requires precise alignment to ensure transmission efficiency.
- Battery Installation: The battery pack is installed in a suitable position on the frame to ensure the balance and safety of the vehicle. The battery connection lines need to be correctly connected to the controller.
- Controller Installation: The controller is the brain of the electric scooter, responsible for controlling the start, acceleration, deceleration, and stop of the motor. The controller is usually installed in a position that is easy to operate.
- Wheel Assembly: The assembly of the front and rear wheels includes the installation and inflation of the tires, as well as the installation of the hubs and brake systems.
- Suspension System Installation: The suspension system includes the front fork and rear shock absorbers, which affect the comfort and handling of the vehicle.
- Brake System Installation: The brake system is a key part of safety and needs to be installed accurately and tested to ensure good braking performance.
- Electrical System Connection: This includes wiring all electrical components, such as lights, signals, horns, etc., and ensuring that all electrical connections are safe.
- Body Shell Installation: The body shell includes plastic parts, such as the front panel, side panels, and rear mudguards, which not only provide protection but also affect the appearance of the vehicle.
- Final Inspection: After the final assembly is completed, a series of functional and safety checks are carried out, including electrical system testing, brake testing, and handling testing.
- Performance Testing: The electric scooter needs to undergo actual road testing to ensure its performance meets the design standards.
- Quality Inspection: Before the vehicle is ready for shipment, a final quality inspection is carried out to ensure there are no missed defects or issues.
- Packaging and Shipping: Vehicles that have passed the quality inspection are cleaned, packaged, and prepared for shipment to dealers or consumers.
The entire final assembly process requires strict quality control and meticulous operation to ensure that each electric scooter meets high standards of manufacturing quality.

The systematic design of an electric scooter assembly line is a comprehensive engineering task that requires consideration of multiple factors to ensure the efficiency and adaptability of the production process. First and foremost, the design team must have a detailed understanding of the user’s workshop dimensions, including available space, floor load-bearing capacity, and any physical limitations that may affect the layout of the production line. This helps in the rational planning of the production line layout, ensuring the reasonable distribution of equipment and workstations, as well as smooth flow of personnel and materials.
Secondly, planning production capacity is key to the design of the production line. Designers need to determine the expected output of the production line based on the user’s production requirements and market forecasts. This involves precise calculations of production pace, the number of workstations, and the required human resources to meet the set production targets.
The level of automation is another important design parameter. With the development of technology, automation can not only improve production efficiency but also reduce labor intensity and production costs. Designers need to assess the user’s technical capabilities and budget, and select appropriate automated equipment and technologies, such as robotic welding, automatic assembly machines, and intelligent logistics systems.
In addition, the systematic design of the production line should also consider the flexibility and scalability of the process. This means that during the design, some space and interfaces should be reserved to adjust or upgrade according to changes in production needs in the future.
Finally, safety and environmental factors are also indispensable in the design. Ensuring that the production line meets safety standards and taking necessary protective measures, such as emergency stop buttons, safety fences, etc., while considering energy-saving and emission reduction and waste treatment to achieve green production.
In summary, the systematic design of an electric scooter assembly line is a complex process that involves consideration of various factors, including workshop conditions, production capacity planning, automation technology, process flow, safety, and environmental factors, to build an efficient, flexible, safe, and environmentally friendly production system.