Small-scale Lithium Battery PACK production line plant

The main process flow of a lithium battery PACK production line includes the selection and matching of battery cells, the assembly of battery modules, the welding of cells, the integration of the Battery Management System (BMS), the assembly of the PACK casing, overall performance testing, and final packaging and shipment. Initially, cells are selected to ensure their performance consistency and then paired according to design requirements. Subsequently, cells are assembled into modules through welding or other connection methods, and the BMS is integrated to monitor the battery status and safety. After that, the battery modules are placed into a custom PACK casing for sealing and fixing. Once the assembly is complete, a series of performance tests are conducted, including voltage, capacity, internal resistance, and cycle life, to ensure the product meets quality standards. Finally, the PACK is packaged and prepared for shipment.
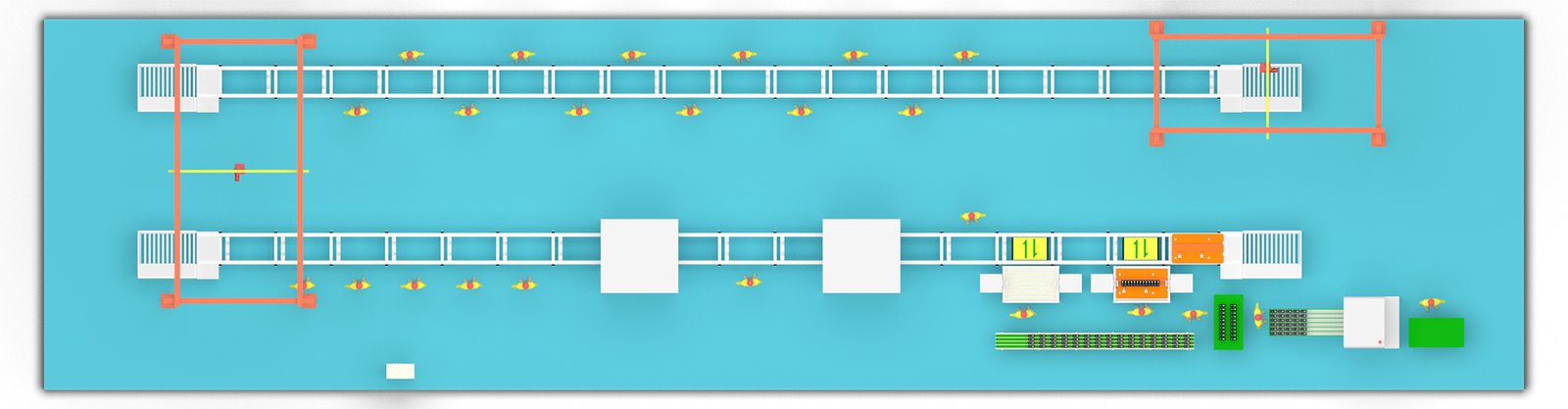
The main process flow of a lithium battery PACK production line involves multiple steps, each equipped with corresponding equipment to ensure production efficiency and product quality. Here is a detailed description of the process and the main equipment used:
- Battery Cell Selection and Matching:
- Equipment: Battery testers, sorting machines
- Process: Conduct charge and discharge tests on battery cells to assess their capacity, internal resistance, voltage, and other parameters, ensuring the consistency of battery performance for subsequent matching.
- Battery Module Assembly:
- Equipment: Automatic assembly lines, welding robots
- Process: Assemble the selected battery cells into battery modules according to design requirements, which may include welding positive and negative connection tabs, securing battery cells, etc.
- Cell Welding:
- Equipment: Laser welding machines, ultrasonic welding machines
- Process: Use welding equipment to join the connection tabs or other components of the battery cells together, ensuring the stability and safety of the electrical connections.
- Integration of Battery Management System (BMS):
- Equipment: BMS testers, programmers
- Process: Connect the BMS module to the battery module, perform programming and testing to ensure that the BMS can accurately monitor and manage the status of the battery.
- PACK Housing Assembly:
- Equipment: Housing assembly machines, sealing equipment
- Process: Place the battery module into the PACK housing, secure and seal it to ensure the overall structural stability and waterproof and dustproof performance of the PACK.
- Overall Performance Testing:
- Equipment: Comprehensive testers, aging test chambers
- Process: Conduct performance tests on the PACK, including but not limited to voltage, capacity, internal resistance, cycle life, charge and discharge performance, etc., to ensure the product meets design and safety standards.
- Safety Performance Testing:
- Equipment: Safety testing equipment (such as overcharge, over-discharge, short circuit, thermal shock testing equipment)
- Process: Conduct a series of safety tests to ensure the safety of the PACK under extreme conditions.
- Final Inspection and Packaging:
- Equipment: Visual inspection systems, packaging machines
- Process: Perform a final inspection of the PACK for appearance and functionality, package it after confirming no defects, and prepare for shipment.
- Quality Control:
- Equipment: Quality inspection systems, data recording systems
- Process: Throughout the production process, monitor production quality through quality inspection systems and record data for traceability and continuous improvement.
These steps and equipment form the core of the lithium battery PACK production line, ensuring efficiency and quality control from raw materials to the final product.
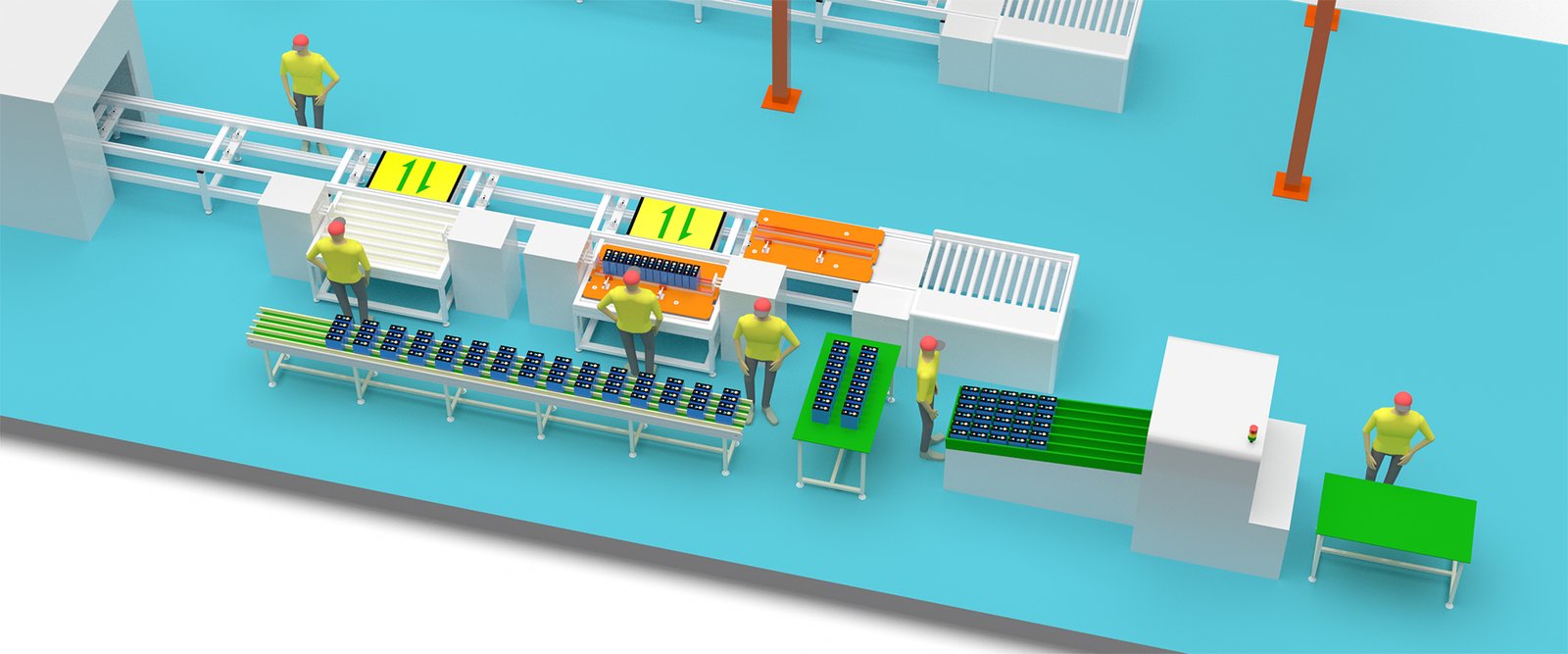
When producing lithium battery PACKs using a production line, the following points should be noted, and there are also several clear advantages:
Points to Note:
- Precise Process Design: Ensure that the process design for each production stage is precise to reduce errors and defects in the production process.
- Quality Control: Implement strict quality control measures at various stages of the production line, including raw material inspection, process control, and final product testing.
- Equipment Maintenance: Regularly maintain and calibrate equipment on the production line to ensure its performance and accuracy.
- Operator Training: Ensure that operators receive proper training to operate equipment correctly and conduct quality checks.
- Safety Measures: Lithium battery production involves certain safety risks, so appropriate safety measures need to be taken, including fire prevention, explosion protection, and electrical safety.
- Environmental Control: The production process of batteries may require controlling environmental conditions such as temperature, humidity, and cleanliness to ensure product quality.
- Material Management: Effective material management and inventory control can reduce waste and costs.
- Flexibility: Design the production line with flexibility in mind to adapt to the production of batteries of different models and specifications.
- Data Tracking: Establish a comprehensive data tracking system for product traceability and quality analysis.
- Compliance: Ensure that the production process and products comply with relevant industry standards and regulatory requirements.
Advantages:
- Improved Production Efficiency: Production line manufacturing can significantly increase production efficiency and reduce production cycles.
- Reduced Costs: Through scaled production, the production cost per unit can be reduced.
- Quality Consistency: Standardized production processes help ensure consistent product quality.
- Reduced Human Error: Automated and semi-automated production lines reduce the possibility of human operational errors.
- Easy Monitoring and Control: Production line manufacturing facilitates the monitoring of the production process and the control of production quality.
- Increased Capacity: The production line can be quickly adjusted to increase capacity according to market demand.
- Flexibility and Scalability: The production line can be adjusted and expanded as needed to meet different production requirements.
- Reduced Space Occupation: Compared to traditional production methods, production line manufacturing is usually more compact, reducing space occupation.
- Improved Worker Efficiency: Operators can focus on specific tasks on the production line, improving work efficiency.
- Environmentally Friendly: By optimizing production processes, energy consumption and waste generation can be reduced, achieving a more environmentally friendly production method.